NICEFLOW® is used in a wide range of industries across all industry sectors. Once again, LEMMA team has been challenged in many benchmarks to prove that there is no need to have a 30 years old compagny to get the best results in marine or off-shore specific sector. NICEFLOW® is now well established as the most full-spectrum and accurate CFD solution, with strong reference on this market.
The numerical basin technology
In a high competitive industrial context, the experimental tests, even at reduced scale, are costly and time consuming for a project : breadboards realisation, tests equipment availability, tests duration and results analysis. Willing to provide efficient innovating solutions within a cost reduction approach, LEMMA has developped the numerical basin concept with its combined expertises in numerical simulation and hydrodynamics.
LEMMA has developed new numerical methods, faster and more accurate, implemented with parallel algorithms in the CFD software NICEFLOW®, which simulates the real turbulent flow of vessels behavior or oil platforms (floating structures).
The numerical performances of the numerical basin enable to seize the reality of physical phenomenon at scale 1. We now are able to
- generate any type of wave : monochromatic, bi-chromatic, regular wave, regular wave packet, irregular waves , within any number of oscillating flaps or spectral methods. Linear or non linear approach considered to generate waves is coupled to RANS or LES-VMS models and allows us to perform very accurate simulations, up to order 6 in space (see example below untitled Numerical investigation of thermally stratified wake).
- take into account current and wind without velocity limitation
- modelise anchors (linear and non linear) linked to floatting bodies
- study sea-keeping and manoeuvrability or non linear roll damping.
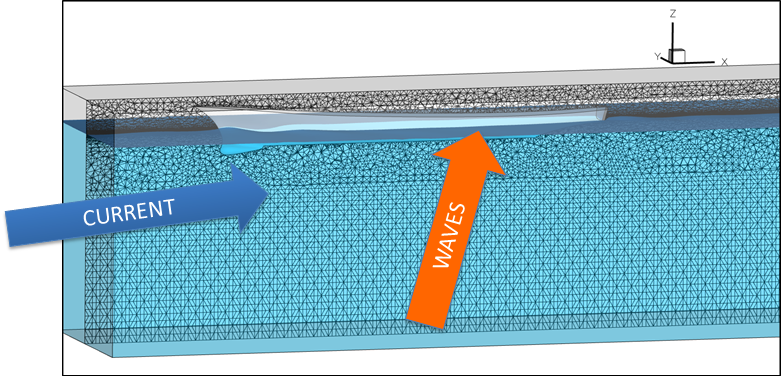
Numerical basin : wave and/or current generation.
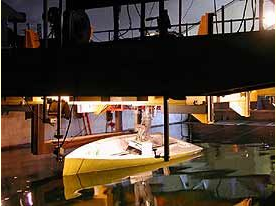
Numerical basin : analytical data.
Main benefits of our technology
Our initial aim was to develop a new technology to get both more accurate results within a time frame divided by 3 to 15 (depending on the application) vs other classical approaches implemented in most of famous other softwares packages. Clearly we want to change the standards in marine and offshore CFD market. How to achieve it ? By combining our background in applied mathematics and our knowledge in hydrodynamics. The method that we use allows us to impose spectral incident waves while reflected waves are calculated using a classical RANS model: that’s the basics of the SWENSE approach initially proposed by the ECN research group (see the picture below).
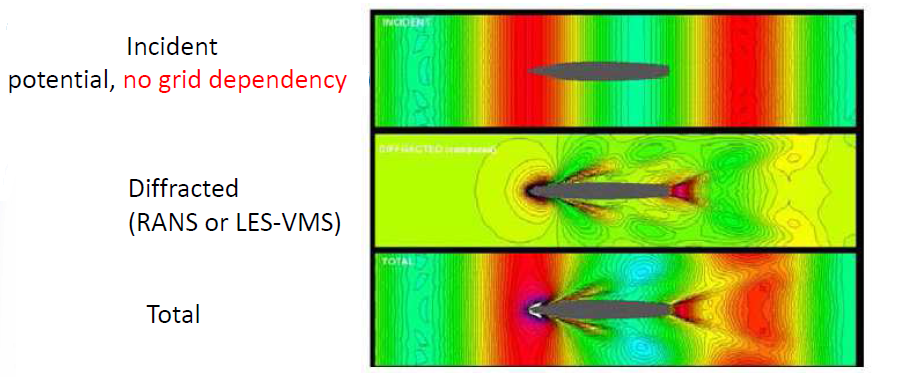
SWENSE decomposition. From R. Luquet thesis, ECN.
Academic validation test cases
3D truncated cylinder in waves
The following simulation on the 3D cylinder takes only three hours on a laptop computer for 18 seconds of physical time (10 periods). The mesh has a complexity of 600 000 nodes. The drag force exerted on the cylinder by impacting incident waves is calculated along time and post processed using a FFT tool. The wave period is 1.8 s, height 0.237 m and steepness is about 4.6%.
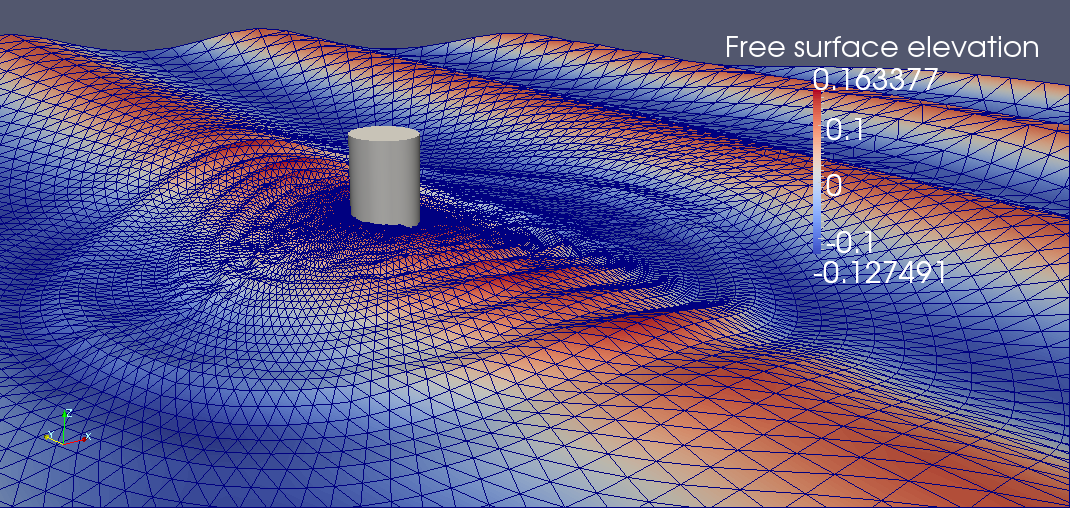
Free surface elevation around the cylinder..
The numerical results are compared with experimental ones (Krokstad & Stanberg, 1995) : the first two harmonics of the drag force are shown on the table below, with a very satisfying agreement.
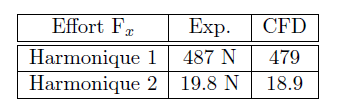
Validation data.

Edge impacting free surface
Initially, the wedge is falling under the gravity and, after the impact, its motion results from its interaction with the water. For this simulation, the geometric mesh adaptation strategy has been applied. A sequence of three quasi embedded meshes containing respectively 3 069, 10 432 and 37 146 vertices has been generated. They correspond to a division by two of spatial step size. This sequence will enable us to study the convergence of the method. During the simulation, when the mesh becomes too distorted due to the displacement of the wedge, the adapted mesh is regenerated with the same geometric and size criteria. CPU time = 6 hours on 1 processor. For further details, see the publication [Allain & al., OMAE 2009]
2D edge impacting free surface, mesh view.
2D edge impacting free surface calculated with improved level set formulation.
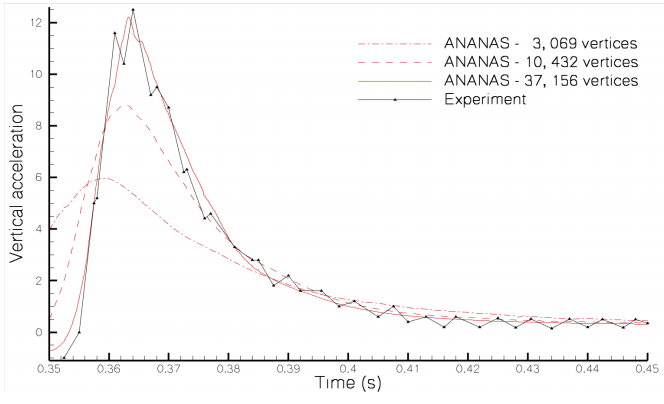
2D falling edge. Plot of vertical acceleration.
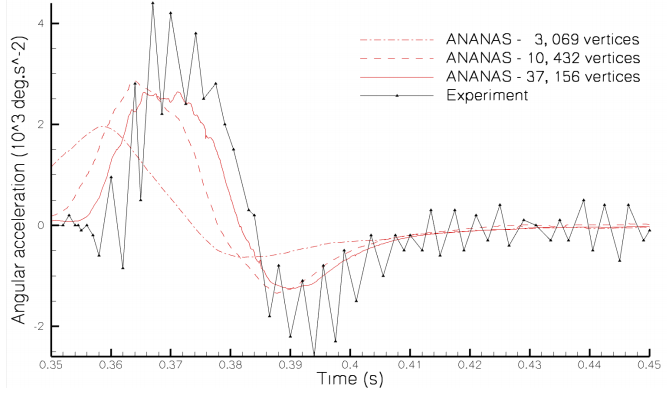
2D falling edge. Plot of angular acceleration.

VIV on multiple cylinders with hybrid RANS-VMS
As a beginning and before simulating VIV problems on multiple cylinders, NICEFLOW® is validated on an academic case dealing with the flow around one cylinder at different Reynolds numbers, ranging from 3900 to 20000. These simulations are performed with our hybrid RANS-VMS model and snapshots are showed on the following pictures. This work has been published in [Computers & Fluids, 2011]. Please ask us if you are interested in this work.
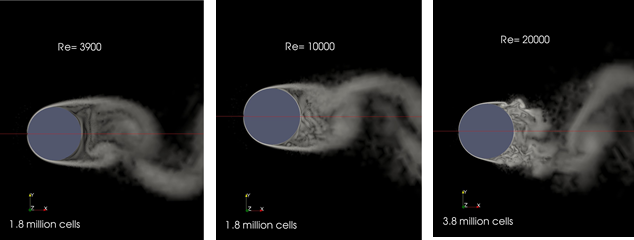
Cylinder at different Reynolds numbers. Hybrid RANS-VMS model.

Marine applications industrial cases
Numerical investigation of thermally stratified wake
For further details about this study, please click here.

Resistance in calm water and added resistance in waves
For further details about this study, performed with ULSTEIN , please click here to download our last scientific paper published on this subject.

Sails performance study
This study shows the potential of intelligent mesh technology to capture the flow around sails. A first Euler calculation around the geometry is done very quickly (5 mn on a laptop) with a coarse mesh of 130 000 nodes. Then we use the intelligent mesh technology to get more accurate results at the design stage, within a calculation of 5 mn on 32 cores. Finally, for the final design stage, RANS calculation is realized by automatically inserting boundary layers around the sails.
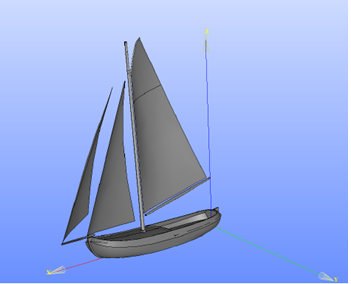
Initial CAD geometry.
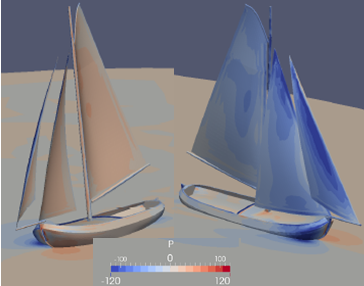
Pressure field on sails – RANS calculation on coarse mesh.
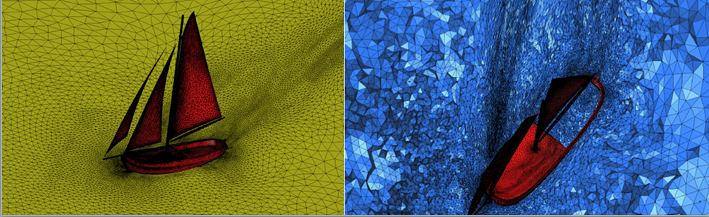
Adapted mesh around sails.
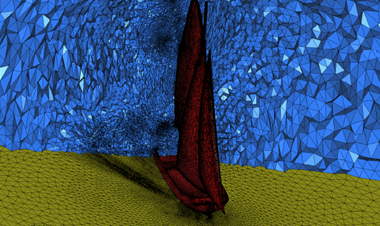
Adapted mesh in the wake.
