LEMMA has strong references in this field and is working with the 8 major companies in this area. For confidentiality reasons, most of our applications can not be shown on this website. The interested reader can also consult the offshore applications page to get an overview of our OffShore/O&G know-how.
- Available models for complex fluid flow modeling
The picture below gives an overview of the different rheological models implemented and validated in NICEFLOW®. These models cover the overall needs of O&G industry and research : viscoplastic flow, viscoelastic fluids at high We number, time dependent thixotropic fluids and multiphase flow).
- Our partner for R&D in rheology and measurements
As measurement technics are also mandatory to accurately identify the constants in the numerical models, LEMMA has a strategic partnership with RHEONIS company, whose expertise and knowledge are based on high-level experienced engineers and research scientists in this field.
- Example : coupling intelligent mesh and viscoplastic flow in sudden expansion
NICEFLOW® is able to compute both newtonian and non-newtonian fluid flows in pipes, at several Reynolds numbers, ranging from stokes flow to fully turbulent (Re=1e7) pipe flow. For turbulent newtonian flows in pipe, many models are available, from RANS to modern and innovative LES-VMS model. Hybrid RANS-VMS can also be used if necessary.
- Example of turbulent newtonian fluid flow in smooth pipe
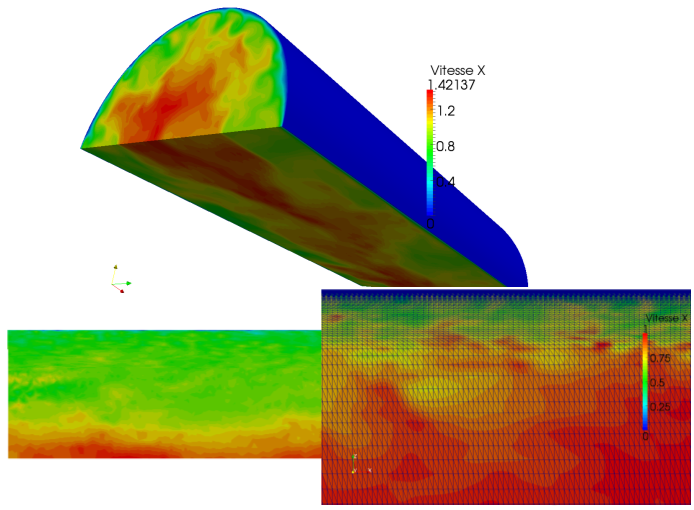
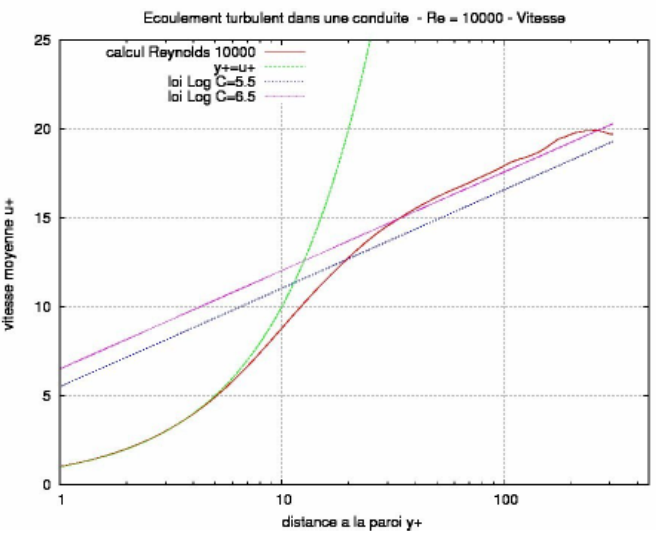
- Paraffinic oil (thixotropic oil flow in smooth pipe)
NICEFLOW® has been used in many practical situations where complex fluid flow are involved and must be solved accurately. The following example (published in [Berton & al, CFM 2011]) gives a good idea of the striking results obtained using intelligent mesh coupled with non newtonian fluid (pseudoplastic with yield stress and thixotropic time dependent rheology) flow simulation. In the first part of the study, a classical spatial convergence is achieved using structured and fixed mesh. The second part shows how intelligent mesh technology allows us to perform a very accurate and converged simulation within less nodes (20% less nodes than M4 structured finest mesh).
The pictures below enable to show the time dependent evolution of the structure parameter used in the thixotropic model (Houska model). In the shear zone near from the wall, this parameter is decreasing, whereas its value remains constant and equal to 1 in the plug flow.
- Two phase wall bounded turbulent flow (LES-VMS & Level-Set formulation)
- Transient PCP (Progressive Cavity Pump) simulation
NICEFLOW® was the first CFD code able to produce full transient 3D simulation of PCP pump within newtonian or viscoplastic fluid. FSI simulation are also performed. This work is published in [Berton & al, SPE Conference 2011]. This was a very challenging case because of the complex geometry and large structure deformation encountered during the simulation. Please see below few snapshots linked to this work , with courtesy of PCM S.A.
Please see below a validation result obtained with a viscoplastic and thixotropic fluid. The flow rate is accurately predicted within an error less than 5%, including uncertainties.
- Lobe pump
Another original case is the lobe pump simulation involving intelligent mesh (mesh is repaired automatically when skewness or size criterion is no longer respected). The prescribed metric allows us to handle transient simulation within very small rotor/stator gap (<0.3 mm). This simulation is shown with courtesy of PCM S.A.
Multiphase flows models have been implemented in NICEFLOW® to produce accurate results depending on the considered physics. Many fields have to be explored in this area, but NICEFLOW® is today able to simulate (with newtonian or non newtonian flows):
- Multiphase flows with particles from low to high concentration (eg. one-way, two way or four-way coupling), with fast eulerian models. See below the turbidity current simulation which is validated with direct numerical simulations (DNS).
- Multiphase flows involving N dispersed phases of rigid particles.
- Multi-scale bubbly flows (improved Level-Set formulation and Rayleigh-Plesset model).
- Emulsion : models derived from kinetic theories are available to quantify emulsion specific area, break-up and collapse, and shape relaxation. Surface tension impact on stress tensor is also included. NICEFLOW® is the unique commercial CFD code having this kind of advanced model. Validation is quite difficult in this case, and it was decided to perform code to code comparisons (NICEFLOW® vs academic research code) to validate this approach. Results are presented below : the flow is laminar at the inlet and the shear stress is calculated at each time step. The model allows us to estimate the shape and droplets orientation in the domain. Blue color enlights area where break up occurs (variation of the droplets specific area).
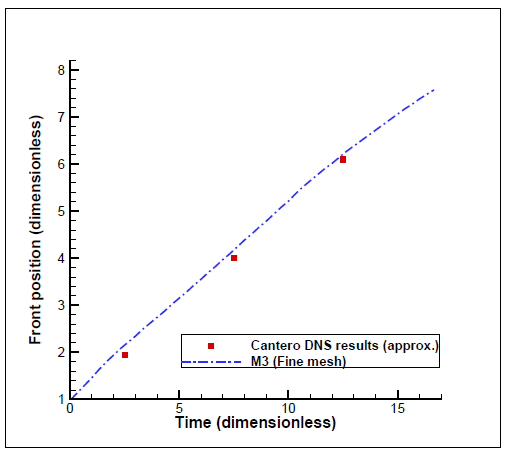
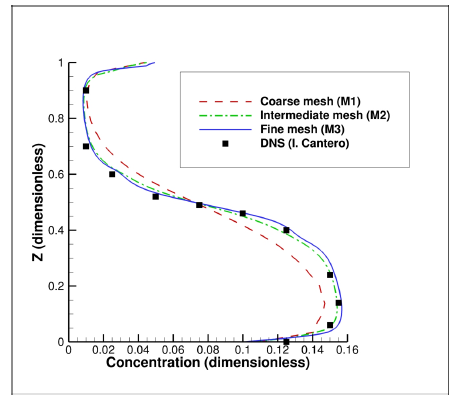
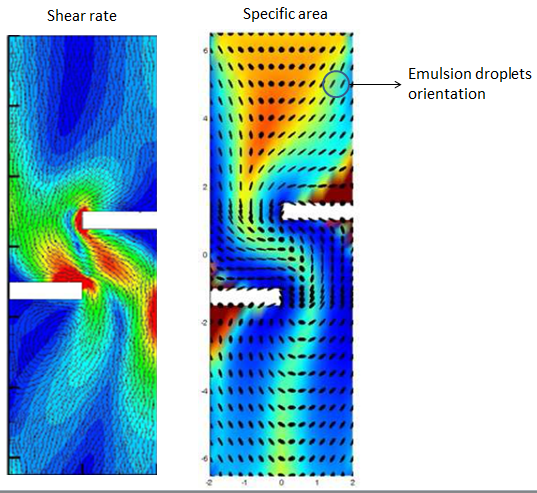
In fact, it is a very hard task to properly quantify if a mixing process can behave as promised. NICEFLOW® is today the only commercial software on the market to provide powerful tools derived from kinetic theory to better understand and predict complex mixing process behavior. We are not talking about time residence simulations (that NICEFLOW® is also able to calculate anyway) to estimate the quality of a blending process. Our innovative tool is a step ahead. It allows the user to directly predict the specific interfacial area, which is by the way one of the most striking quantity available and calculated with NICEFLOW® to estimate the quality of a blend. See below an example : a 2D academic test case (Peclet number =100) to illustrate NICEFLOW® capabilities in predicting good and poor mixing areas.